Joskin combines ArcNC with 3D scanning to increase productivity
The Joskin Group is an European leader in agricultural transport machinery, with a wide product range including slurry tankers, spreading tools, livestock trailers, tippers, silage boxes, and more. After 15 years of programming their welding robots manually, they are now switching to ArcNC to drastically reduce the programming time.
With factories in Belgium, France and Poland (and a new one opening in Esch-Sur-Alzette in Luxembourg later this year), Joskin operates at the forefront of manufacturing automation with a wide range of in-house production capabilities: from laser cutters for metal sheets and tubes, turning and milling cells with robotic manipulator and bending machines, to welding robots.
Their 17 welding robots produce a variety of parts, from smaller assemblies up to whole trailer bodies. Custom jigs are also designed and manufactured in-house.
The parts are then painted or galvanised (the facility in Poland is home to a hot-dip galvanisation line) before they are being dispatched to the assembly lines.
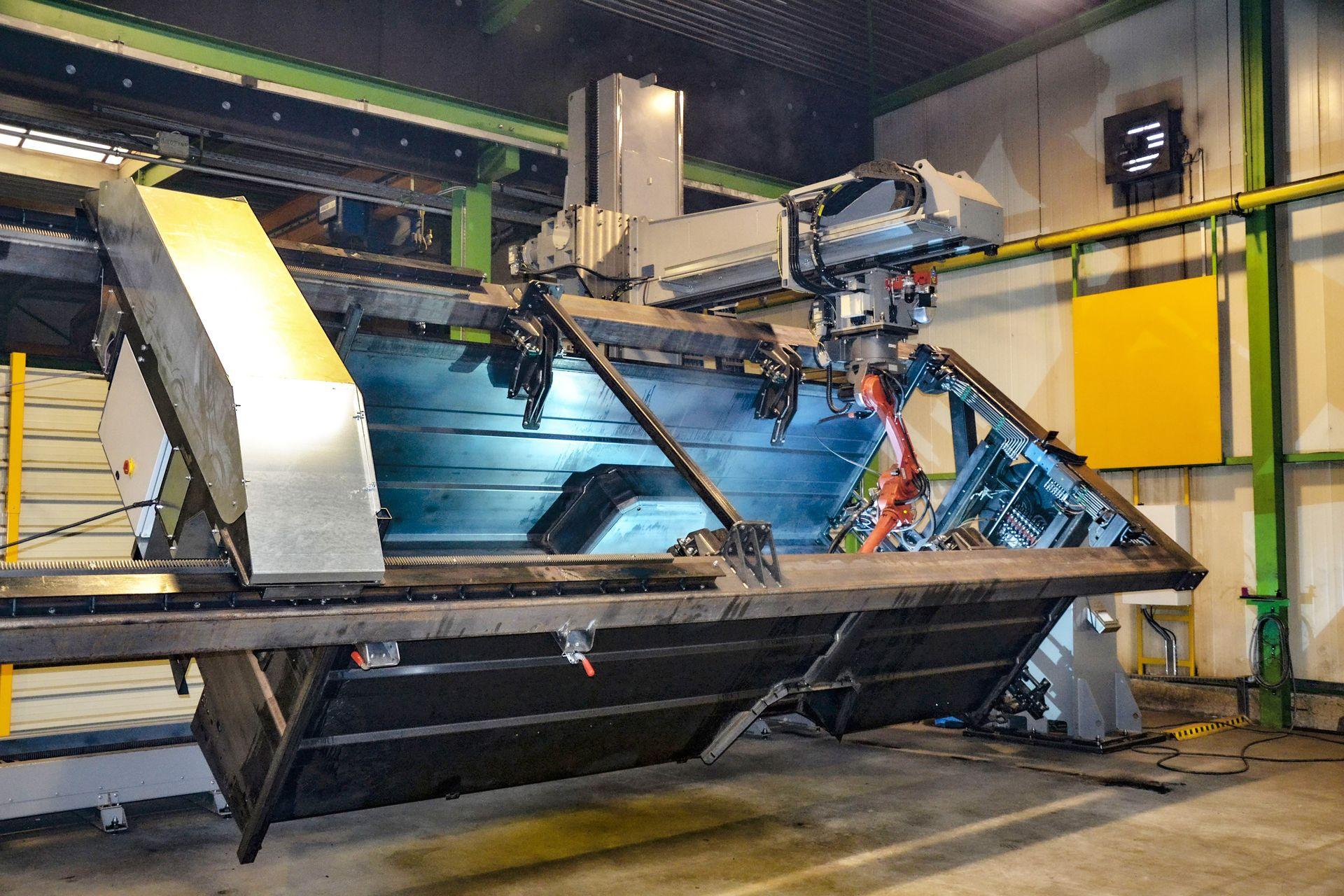
One thing that previously kept Joskin from using automated robot programming is the fact that they do not have their jigs available as 3D drawings. Without these, the software does not know where the stops, clamps, and other elements holding the part are, all obstacles the robot must avoid.
To solve this issue, they now use a Creaform Handyscan 3D scanner to scan the jigs and create accurate 3D models. These models are then used by the ArcNC software to automatically avoid collisions.
The biggest advantage of ArcNC? “The automatically generated search motions,” replies Guillaume Balthasart - process engineer at Joskin - without hesitation. “Previously, we manually touched up the program at the start of every new batch. The automatic search motions save us a lot of time, and guarantee perfect welds every time.”
They started using ArcNC on their two newest robots, but this is only the beginning. “The goal is to program all robots with ArcNC and achieve tenfold gains in programming time across the board, especially for the very large complex parts,” says Didier Joskin.
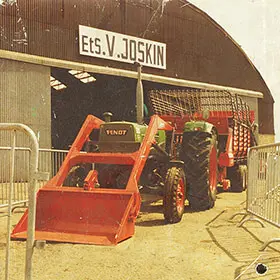
Located in the heart of the Entre-Vesdre-et-Meuse region, in Herve country, east of Liège in Belgium, a grassy agricultural plateau known for its Herve cheese. This is where the headquarters of the Joskin Group is located, a company that has made a name for itself in agricultural machinery. “It was my father, Victor Joskin, who founded the company in 1968, initially an agricultural contracting business, thanks to the equipment of my grandparents’. My father then invested in his own equipment to strengthen the fieldwork service offered to other farmers,” recalls Didier Joskin, CEO and production manager of the group.
But Victor Joskin didn’t stop there. He then repaired his own machines, then those of his clients, which led him to open a real repair service, and then he imported equipment that was not available in the region. Gradually, the range of distributed brands expanded, and the company then abandoned agricultural contracting to focus on repairing and importing machines. Didier Joskin continues: “In 1984, in a difficult economic context, my father decided to produce his first slurry tanker to continue offering his clients machines at reasonable prices. And just a few years later, the company had its first production plant.”
Today, the group employs over 870 people with an annual consolidated turnover of 140 million euros across five production sites in Soumagne and Thimister-Clermont (Belgium), Trzcianka (Poland), and Bourges and La-Vieille-Lyre (France).