Gamechanger for Robotic Welding
Original article in Blechtechnik by Ing. Norbert Novotny, x-technik
In the Binderberger Maschinenbau GmbH factory, welding robots have been used for some time, but until now, they were manually programmed at the machine. With the new ABB robotic welding cell, programming is now done offline for the first time using the advanced ArcNC welding software, which can be easily operated even by users with no prior knowledge of robot programming. This development has brought welding technology at Binderberger to a new level, resulting in a significant increase in efficiency and time savings.
Binderberger Maschinenbau GmbH, located in St. Georgen am Fillmannsbach in Upper Austria, designs and manufactures high-quality machines and equipment for timber harvesting and processing. Nearly seven decades of experience with wood-processing companies, farmers, and forestry operations feed directly into the development and expansion of their product range. "From timber trailers and grapple loaders to circular saws, wood splitters, and conveyors, we offer a comprehensive range of high-quality products for working with wood. We have now become one of the leading full-service providers for firewood transportation, production, and processing," explains Production Manager Matthias Wasner, M.Sc.
The company operates an extensive machine park, allowing them to handle a large portion of production in-house, enhancing flexibility and dynamism. "We have mastery over processes like laser cutting, tube laser cutting, punching, bending, welding, and mechanical manufacturing, including turning and milling. This makes us largely independent and keeps quality control in our own hands," Wasner says. With a high degree of automation, Binderberger tackles the shortage of skilled workers and can strategically deploy its 70 employees where human expertise, flexibility, creativity, and judgment are needed.
For more than 25 years, Binderberger has relied on industrial robots for welding. Recently, the two existing welding robots were supplemented with a new, cutting-edge robotic welding cell from ABB. "Over the years, ABB’s robots have performed reliably, and our collaboration, especially with their service, has been highly professional. So, it was clear to us to choose ABB again for the new system," emphasizes Wasner.
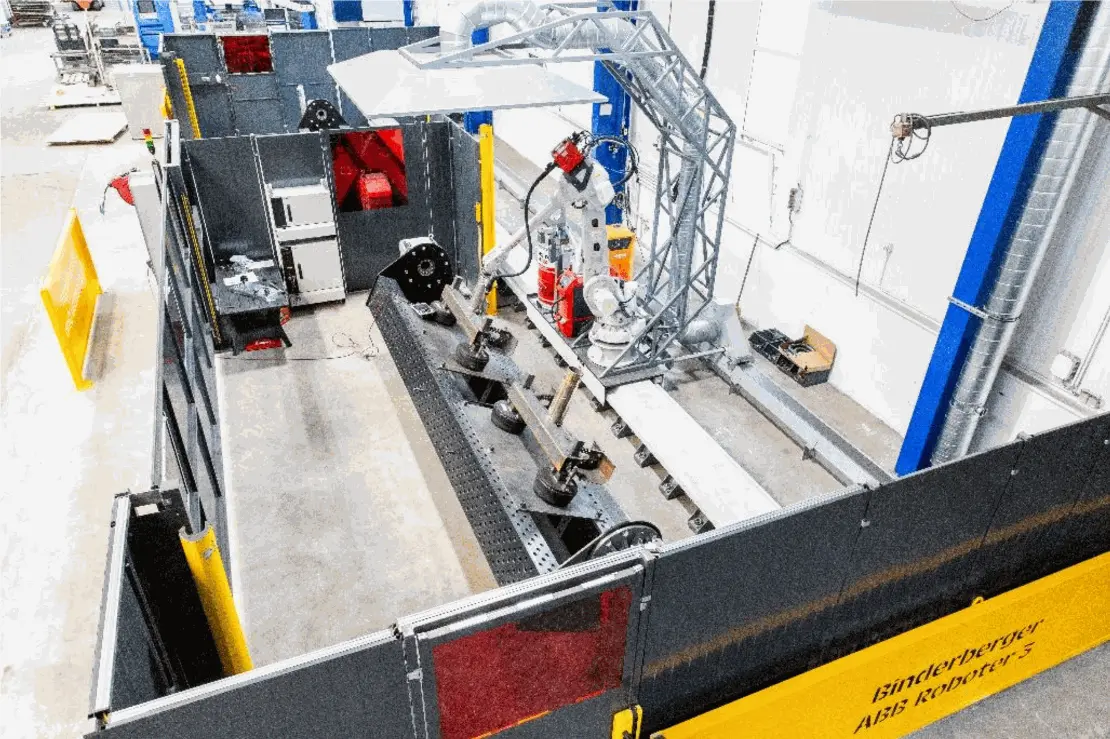
Designed for the production of base frames for timber trailers, the new ABB robotic welding cell can weld parts up to five meters in length. (Images: x-technik)
Automated welding of frame structures
The new ABB welding cell is designed for the production of base frames for timber trailers, capable of handling parts up to five meters in length. Binderberger's timber trailers are powerful and reliable tools for transporting logs, excelling in challenging forestry operations on difficult terrain. Stability and high-quality craftsmanship are crucial. "Until now, we manually welded all 300 of these base frames, each up to 4.3 meters long, that we need annually. Now, the robot handles this task far more efficiently and delivers consistently high quality, regardless of the operator's welding skill," Wasner explains with satisfaction.
The system features two identical positioning tables, enabling a two-station operation. While one station is being set up, the robot welds the previously hand-tacked frames at the other station. The welding robot moves along a 15-meter track to switch between the stations. The system includes not only the robot but also the power supply for the welder, wire feed, and an exhaust hood. "The mobile exhaust hood allows us to load and unload the heavy frames onto the positioning tables using the overhead crane," adds Wasner. The welding cell also features automatic torch cleaning and measurement.
"We chose the IRB 4600 robot with a 2.5-meter reach to accommodate parts with a diameter of up to 2.3 meters," explains Martin Moosbacher, Project Manager at ABB Robotics in Austria. Binderberger uses precision Siegmund perforated tables as base fixtures on the positioning tables, allowing for the precise mounting of various parts. The combined weight of the fixture and the timber trailer base frame—about 4,000 kg—was carefully considered in the load capacity of the positioning tables. "Both sides of the positioning tables are synchronized to ensure precision and avoid deformation under such heavy loads," Moosbacher explains in detail. Besides producing the timber trailer base frames, the new robotic welding cell also has the capacity to relieve the workload of the existing welding robots. "We can also clamp and weld multiple parts consecutively on the larger system," Wasner adds.
Without any robot programming knowledge, programs for the welding robot can be created using the ArcNC welding software.
Impressed by the simplicity and completeness
Initially, Binderberger did not plan to program the new welding cell offline. "However, after seeing ArcNC welding software in action at a neighboring company, I was very impressed and wanted to use it for our new system," recalls Wasner. Both Wasner and Moosbacher were captivated by ArcNC after a demonstration at ABB in Wiener Neudorf, where a sample part was programmed and welded. "We’ve never seen welding software as complex and complete as ArcNC. With no need for robot programming knowledge, users can easily create welding programs through a simple graphical interface. The software not only detects potential weld seams and generates the necessary robot paths but also calculates collision-free routes for the robot to approach and leave the workpiece," Moosbacher explains.
The robot is equipped with a wire brake, essential for precise seam detection to automatically detect start and end positions of welds. This made ArcNC a perfect fit for the new welding cell. The software was also retrofitted to one of Binderberger's existing welding robots. "These are highly automated systems with robots, external axes, and positioning tables, and ArcNC handles all these movements with ease," says Moosbacher, clearly impressed.
Perfect collaboration in robotic welding (from left to right): Daniel Pichler (ArcNC), Matthias Wasner (Binderberger), and Martin Moosbacher (ABB).
Designed specifically for welders
"Our software was designed specifically for welders, so they don’t need to worry about axis movements or robot singularities. With a simple interface that lacks hidden menus or buttons, welders can start using ArcNC to create programs and run simulations in just two hours," says Daniel Pichler, Sales Director of ArcNC. "The algorithm identifies potential weld seams and calculates the weld paths and all secondary movements automatically." Typically, offline programming compensates for tolerances in the precision of the robot, workpiece, or other system components by using time-consuming search routines. ArcNC automates this process. Due to the immense computing power required for these calculations, ArcNC was developed as a cloud-based solution.
In addition to the ease of program creation, Wasner sees another major advantage: "In the simulation, I can already detect potential issues, which the system alerts me to with warnings." He also appreciates the time savings from offline programming: "Previously, we had to clamp the part and program it directly at the machine, while the robot was idle. Those unproductive times are now a thing of the past." ArcNC has also significantly improved accuracy in the older welding cell. "We used to have issues when tacking wasn’t done precisely. Now, the system measures exact positions in advance, reducing the need for rework." Pichler adds that ArcNC makes it easy to transfer completed programs to different welding cells: "ArcNC recalculates all paths for the specific system, and only minor adjustments for accessibility might be necessary."
Timber trailers from Binderberger handle even challenging forestry tasks with excellence and reliability.
Great potential for ArcNC
Looking back, Wasner is extremely satisfied with the collaboration with ABB and ArcNC: "Both companies did everything right on this project. Communication has always been on an equal footing, and questions are answered quickly and competently." Moosbacher also sees great potential for the future: "Traditional offline programming requires a robot specialist with extensive programming and welding knowledge. With ArcNC, that’s no longer necessary. This software truly has the potential to be a gamechanger in the world of robotic welding."