The fastest way to program welding robots
In the world of industrial robotics, programming welding robots has traditionally been a complex and time-consuming process. The programming methods have evolved significantly over the years, each offering different advantages and challenges.
In this blog post, we will explore the traditional ways of programming welding robots, including online programming using teach pendants and cobots, as well as offline programming (OLP).
We will explain how ArcNC's automated programming approach stands apart from these traditional techniques, offering a more efficient, user-friendly, and cost-effective solution specifically designed for welding applications.
Online Programming
Online programming involves programming the robot directly on the production floor, making it a hands-on approach that provides immediate feedback. This category of programming includes using teach pendants and cobots, each of which offers its own set of benefits and limitations.
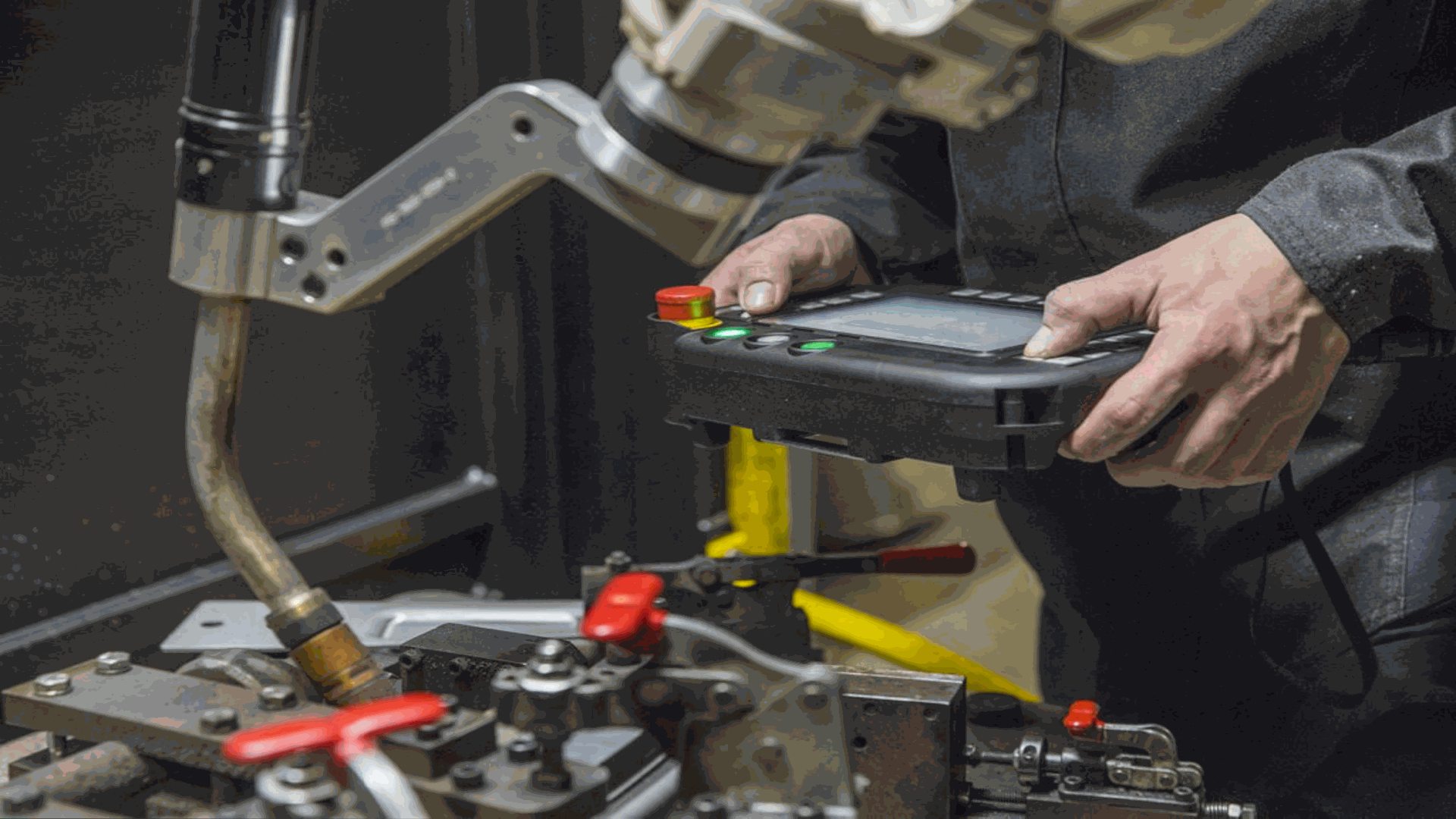
Teach Pendant Programming
Teach pendants are handheld devices that operators use to manually guide robots through their intended paths and sequences. This method is widely used for industrial welding robots because it allows operators to see the robot's movements in real-time, providing a clear understanding of the welding process. The hands-on nature of teach pendant programming makes it accessible, as it does not require additional software or specialized skills beyond basic manual controls.
However, this method can be incredibly time-consuming, particularly when programming complex motions such as search motions or coordinated movements. Moreover, since the robot is occupied with programming, it is not welding during this time, leading to significant downtime and reduced productivity.
Teach pendant programming is most suitable for getting started with basic welding tasks, handling simple parts with few welds, or fine-tuning existing programs by adjusting parameters or touching up welds. It is an effective entry-level method but becomes less practical as the complexity of the welding tasks increases.
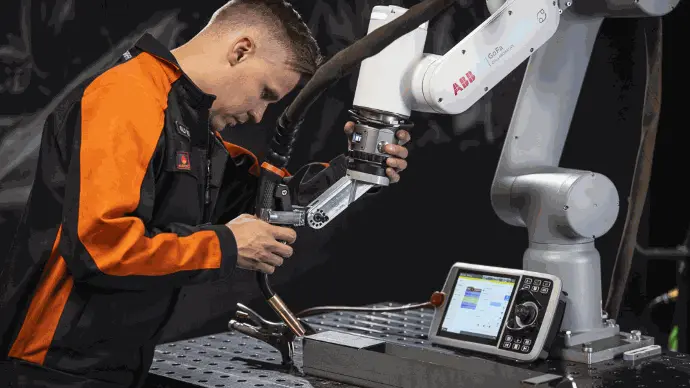
Collaborative Robots
Cobots, or collaborative robots, were first introduced by Universal Robots in 2008, and since then, most major robot manufacturers have developed their own versions. Cobots offer a more intuitive programming experience, allowing operators to physically move the robot into the desired positions for basic tasks. This intuitive "grab and move" feature makes cobots easy to deploy and user-friendly, especially in smaller workspaces where they can be table-mounted and do not require safety fences.
Despite these advantages, cobots share similar drawbacks with teach pendants, including being time-consuming and causing robot downtime during programming. Moreover, cobots often lack advanced welding capabilities, such as integrated manipulators and rails, touch sensing, and seam tracking, limiting their utility in more complex welding applications.
Cobots are best suited for environments with space constraints and for handling small, simple parts where the absence of advanced welding features is not a significant limitation.
Offline Programming
Offline Programming (OLP) provides an alternative to online methods by allowing users to create robot programs on a computer, away from the production floor. This approach encompasses a wide range of solutions, from basic robot simulators to advanced software with welding-specific features, developed by both robot manufacturers (eg. Panasonic DTPS, Yaskawa MotoSim, ABB RobotStudio, Cloos Roboplan, or KUKA.Sim) and third-party companies (such as Visual Components, FastSuite, Almacam, Octopuz, or RoboDK).
The primary advantage of OLP is that it eliminates robot downtime; programs are created offline, allowing robots to continue welding uninterrupted. Additionally, OLP is versatile and can be used for various applications beyond welding. However, these benefits come at a cost. OLP systems are often complex to use, featuring a steep learning curve that requires trained engineers to operate. Developing detailed programs can still take considerable time, offsetting some of the efficiency gains from eliminating robot downtime.
OLP has traditionally been used when tasks are time-critical, highly optimized, or require virtual commissioning and integration with other hardware, such as conveyor belts or feeding mechanisms. However, for most welding applications, especially those involving less complex or more varied tasks, OLP is increasingly being replaced by more streamlined solutions like automated programming from ArcNC.
Automated Programming with ArcNC
ArcNC introduces a new paradigm in robot programming, specifically tailored for welding applications. Unlike traditional OLP solutions, ArcNC automates most of the programming work, making it significantly more user-friendly and efficient.
Designed for Welders
Designed with welders in mind, ArcNC requires only two hours of training for operators to become proficient, compared to several days for traditional OLP systems. This ease of use is a significant departure from traditional methods, where operators need to be knowledgeable in welding, robotics, and programming. With ArcNC, the only prerequisite is expertise in welding, greatly simplifying the process and lowering the entry barrier.
ArcNC | Traditional OLP | |
Supported applications | Welding | Any / many |
Training requirement | 2 hours | Multiple days |
Skills required | Welding | Robotics + programming + welding |
ArcNC | Traditional OLP | |
Supported applications | Welding | Any / many |
Training requirement | 2 hours | Multiple days |
Skills required | Welding | Robotics + programming + welding |
Advanced Automation
ArcNC leverages advanced automation to streamline the programming process. Robot motions are automatically generated, eliminating the need for manual specification required in OLP. Collisions are avoided automatically, and search motions are generated without manual input. Additionally, welds are automatically extracted from CAD models, and programs are immediately ready to run on the robot, without the need for manual adjustments often required by traditional OLP systems.
ArcNC | Traditional OLP | |
Starting price | € 7,000 | € 15,000 - 35,000 |
Average time spent to generate program | < 1 hour | > 1 day |
Minimum batch size | 1 - 5 | > 50 |
ArcNC | Traditional OLP | |
Automatic weld extraction | ✔ | ✘ |
Collision detection | ✔ | ✔ |
Automatic robot motion planning, | ✔ | ✘ * |
Automatic search motions generation | ✔ | ✘ |
Output ready to run on the robot without manual adjustments | ✔ | ✘ |
ArcNC | Traditional OLP | |
Automatic weld extraction | ✔ | ✘ |
Collision detection | ✔ | ✔ |
Automatic robot motion planning, | ✔ | ✘ * |
Automatic search motions generation | ✔ | ✘ |
Output ready to run on the robot without manual adjustments | ✔ | ✘ |
ArcNC | Traditional OLP | |
Starting price | € 7,000 | € 15,000 - 35,000 |
Relative time spent to generate program | 1 | 8 |
Minimum batch size | 1 - 5 | > 50 |
Profitable for Small Batch Production
This high level of automation makes ArcNC particularly profitable for small batch production. With a starting price of just € 7,000, ArcNC provides a cost-effective alternative. Programs can be generated within hours rather than days, and the solution is suitable for batch sizes as small as 1–5. This makes ArcNC an ideal choice for a wide range of welding applications, from small-scale operations to more extensive production runs.
(*) a few traditional OLP solutions (eg. Fastsuite & Visual Components) also provide tools for more automated motion planning
A short note on scanner-based solutions
While discussing different programming methods, it's also important to mention scanner-based solutions offered by companies like Abagy, and Path Robotics. These systems use scanners to detect weld paths automatically and program the robot accordingly. However, this approach comes with significant limitations.
The need for additional hardware increases costs and complexity, and when scanners are mounted on the robot, they can reduce freedom of movement and affect reliability. Furthermore, scanners can struggle with occlusions and reflections, leading to inaccurate data that can result in missing or faulty welds or even collisions. Scanner-based solutions are also typically limited to less complex parts, often supporting only 2.5D welding tasks (welds on planar surfaces). They frequently require reprogramming when introducing new part families, which can diminish their efficiency in dynamic production environments.
Conclusion
The landscape of programming welding robots is diverse, ranging from traditional online methods like teach pendants and cobots to more advanced offline programming (OLP) solutions. Each method has its place, depending on the specific needs and constraints of the application. However, they often come with significant trade-offs in terms of time, complexity, and cost.
ArcNC's automated programming solution offers a significant advancement in welding robot programming, providing a faster, easier, and more cost-effective alternative. By focusing specifically on welding, ArcNC simplifies the programming process, reduces training requirements, and minimizes the need for expertise beyond welding. With its ability to quickly generate ready-to-run programs, automatically avoid collisions, and optimize robot movements, ArcNC is a game-changer for both small batch production and large-scale operations.
